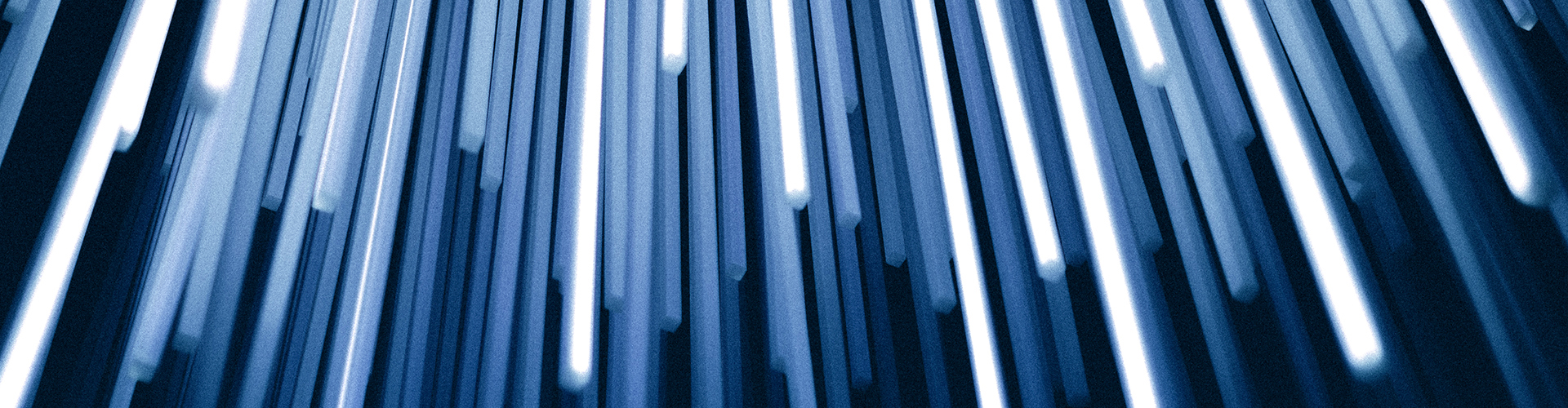
Paper sessions & workshop A
Paper sessions A:I-A:V April 24th, 10:00-12:00
A:I Sustainable Manufacturing
Room: C118. Session Chair: Alexander Kaplan. Room Host: Achmad Ariaseta
A concept from sensor to sustainability in machining – An interdisciplinary approach over a wide TRL range
Jan-Eric Ståhl, Anders Mikkelsena, Filip Lenricka, Maria Sandstena, Anna-Karin Alma and Christina Windmark.
Abstract
This publication describes a concept that intends to enable an optimization of machining with regard to the balance between criteria related to technology, economy and sustainability. The work is of a discussion nature and intends to provide a framework for further research and development in the area. Previous research and development during the 80’s and 90’s is presented in general terms and in particular the reasons for its limited success in providing real-time feedback on machining operations are highlighted, despite very large financial investments even by today’s standards. Ongoing research worldwide in current process optimization and its associated building blocks will be highlighted, and identified important work is referenced. Below are new conditions that can be linked to both process knowledge and its modeling, as well as new conditions for developing integrated sensors that can handle the extreme environment in and around a processing operation. A previous limiting factor has been signal processing and signal transmission, which with new knowledge and developed technology in the last 10 years provides new conditions for process optimization in real time.The need for new and up-to-date principles for process optimization, which also integrate sustainability issues and environmental impact, has increased in importance in several respects. Important issues such as tool utilization, efficient use of materials and high time utilization have become relevant as these process results control both energy consumption and environmental impact. The geopolitical development linked to the availability of critical tool materials such as cobalt and tungsten also drives research issues that can generally optimize and streamline production processes.Finally, the publication describes the possibility of realizing a real-time feedback and optimized machining that takes into account technology, economy and sustainability, through interdisciplinary research across several levels of technology readiness (TRL). The results are expected to have positive effects on several production factors before, during and after machining. Developed technologies in machining can also make valuable contributions to the development of other products and production processes.
Study of pulsed laser beam welding of nickel-based superalloy G27
Achmad Ariaseta, Dario Pick, Joel Andersson and Olanrewaju Ojo
Abstract
The influence of pulsed laser beam welding (LBW) parameters on the weld geometry and imperfections of a new nickel-based superalloy called G27 was studied by a statistical design of experiment, and the microstructures of the weld fusion zone (FZ) of the pulsed laser beam-welded G27 were characterized. No evidence of cracks is found in the FZ and heat-affected zone (HAZ). Other weld imperfections, such as undercut and underfill, were also hardly observed. The pulse factor significantly influenced all the responses, i.e., minimum weld width (Wm), root excess weld metal, and average pore diameter, whereas welding travel speed significantly influenced Wm and root excess weld metal. Power and interaction between pulse frequency*pulse factor were statistically significant in influencing the root excess weld metal and average pore diameter, respectively. The pulse frequency and interactions between power*travel speed, power*pulse factor, power*pulse frequency, travel speed*pulse factor, and travel speed*pulse frequency did not significantly influence any response. Microsegregation pattern that occurs during weld solidification leads to the formation of Nb-rich MC carbides and Nb-rich Laves phase as the major secondary phase constituents in the FZ of as-welded G27. The presence of brittle Laves phase requires careful consideration when developing suitable post-weld heat treatment of G27.
Relationship between tool temperature distribution and stagnation point behavior for different process factors in machining operations
Jan-Eric Ståhl, Maria Strömberg Bylund, Per Alm and Vyacheslav Kryzhanivskyy
Abstract
Metal cutting is physically defined by a tool separating a chip by developing a stagnation point after the work material has passed a shear plane. This distinguishes the method group metal cutting or machining from shearing and wedging processes. The development of the stagnation point is central to the functioning of a metal cutting process. The stagnation point and its behavior has a great influence on the different load conditions of the tool as it controls both the temperature distribution and the mechanical load distribution around the tool’s edge-line. This publication shows that there is a temperature drop at the stagnation point where the shear stress changes sign, which means that the shear stress at this point assumes the value zero. Furthermore, it is demonstrated that there is a correlation between the position of the temperature dip, its size and the selected cutting data as well as tool geometry and current work material. The knowledge of the interaction between the position of the stagnation point and the tool coating type in combination with the tool’s micro- and macro-geometry will be of importance for the development of high-performance tools optimized for different machining applications.
Effect of Laser Power on the Deposition of Alloy 718 Powder on Alumina Substrate using Laser Directed Energy Deposition: A Single-Track Study
Dilipkumar Choudary Ratnala, Fabian Hanning, Joel Andersson and Shrikant Joshi
Abstract
Welding or brazing of metals to ceramics often leads to failures under aggressive conditions due to abrupt changes in physical, chemical, and thermal properties at the metal-ceramic interface. Metal-ceramic Functional Graded Materials (FGMs) replace the strict interface with a gradual transition of composition and properties, which protects the material from failures. The powder-blown Laser-Directed Energy Deposition (DED-LB) is one of the widely known Additive Manufacturing (AM) processes that offer unique features like developing FGMs and multi-material structures. Various studies have been conducted to process metal-ceramic FGMs using the DED-LB process but significant differences in thermal properties, varying laser-material interactions, and the possibility of formation of complex reaction products make the processing of metal-ceramic FGMs challenging. This study aims to understand the effect of laser power on a ceramic substrate, and its interaction with a metal powder introduced in the melt pool. A single track of nickel-based superalloy Alloy 718 powder was deposited on an Alumina substrate with different laser powers. The deposition was performed with and without substrate pre-heat to understand the effect of pre-treatment on deposition. Metallographic analysis was performed to reveal the microstructure of the resolidified metal mixed ceramic region.
Multi-variate analysis of laser powder bed fusion with 90-μm layer thickness of Ni-based superalloy Haynes 282
Kameshwaran Swaminathan, Saadat Ali, Jonas Olsson, Tahira Raza, Peter Harlin and Joel Andersson
Abstract
Laser powder bed fusion (PBF-LB) processing of Haynes 282 using a layer thickness of 90-μm is studied for process capability and feasibility for increased productivity. To optimize the build rate while producing metallurgically sound parts, the effect of laser parameters on the resulting melt pool dimensions and porosity are analyzed. In a previous study, individual parameters such as laser power, scan speed and hatch distance and combination have been studied. In this study, three levels of hatch distance have been investigated while varying power and speed to same extent at all three (3) hatch distance. Similarly, the highest power level has been studied for the effect of speed and hatch distance. The melt pool dimensions, and porosity were measured in the plane parallel to the build direction. Comparison of measured responses with individual parameters provides partial trends of melt pool dimensions and porosity. It was observed that high power and/or low speed and low hatch distance increase the melt pool dimensions and reduce porosity until keyhole mode is reached. Variation of two parameters while keeping the third parameter constant was found to affect porosity due to the transition from lack of fusion type defects to keyhole porosities. The presence of dominant type of defect is identified using average feret ratio, which is the ratio of maximum length to minimum length across parallel surfaces inside a defect. It is found successful to use the combination study of process parameters and resultant type of defects to map the process to achieve minimal defects is identified for 90-μm layer thickness, through the combination study of process parameters and the resultant type of defects.
A:II Smart Production and Automation
Room: C120. Session Chair: Dan Högberg. Room Host: Anders Nilsson
Anomaly detection in optical monitoring of laser beam welding
Morgan Nilsen
Abstract
Robotized laser beam welding is one important process in manufacturing, offering efficient welding while minimizing the heat input. Nonetheless, this method is sensitive to various deviations, including fixture problems, heat-induced distortions, and inaccuracies in tool handling. Such deviations can lead to significant defects like lack of fusion, particularly when welding square butt joints without gaps. Detecting these defects through visual inspection or non-destructive methods is challenging. To address this, real-time monitoring and automatic intervention are necessary. One effective sensor for monitoring laser beam welding is the photodiode, which captures optical emissions from the process. Research has demonstrated correlations between these emissions and process stability. Photodiodes are cost-effective and easily integrated into welding tools, making them ideal for industrial applications. However, the challenge lies in analyzing the output signals and defining thresholds for identifying deviations from normal conditions. Thus, there’s a need for an automated method to set threshold values based on measured data. Machine learning offers a solution, particularly through supervised, unsupervised, or semi-supervised methods. Supervised machine learning requires labeled data, involving time-consuming experiments with nominal and deviating cases, making it less feasible for industrial setups. This paper suggests using unsupervised learning for anomaly detection, relying solely on data from nominal welding cases for model training. In this approach, a model is trained using photodiode data from a single nominal weld case and subsequently tested on data collected during experiments involving laser beam offsets during welding. The results demonstrate the promise of this method for monitoring closed square butt-joint laser beam welding, even with limited training data from nominal cases.
Exploring the Synergies of Modularization, Interface Standardization, and Service-Orientation in Production System Simulation
Martin Birtic, Pablo Morilla Cabello, Ángel Munoz Rocha and Anna Syberfeldt
Abstract
Production systems of the future may be in constant flux and reconfiguration, continuously adapting to changing production conditions. Digital models and simulation are powerful tools that can be used for their design and operation. These models must co-evolve with the physical system to sustain their usefulness and relevance. This poses a significant barrier, given the complexities involved in their efficient creation and maintenance. To understand whether certain system design concepts make the simulation process easier, this study aims to investigate a combination of concepts that promote reconfigurability and flexibility to explore whether they can positively influence the simulation process. By integrating modularization, interface standardization, and a service-oriented architecture it is believed to support faster and easier creation and updates of digital models. Modularization enhances flexibility by decomposing complex systems into independent, interchangeable modules. Standardizing interfaces ensures uniformity and compatibility among modules. Using a service-oriented architecture entails the encapsulation of various functionalities within modules as services, which can be dynamically requested. Shedding light on the advantages arising from modeling and simulating systems adhering to the mentioned concepts the research also aims to lay the groundwork for further investigation into the potential synergies of these promising production concepts. The study’s methodology includes modeling and programming of industrial robotic production modules adhering to predefined physical and logical interfaces. Interoperability and service orchestration are achieved through a service-oriented architecture. A simulated Manufacturing Execution System is integrated to facilitate handling of module services, product data and service requirements. Finally, a specialized software plugin was developed to support rapid module instantiation into a production system for evaluation. Results suggest that using a modular approach may ease modelling and simulation efforts and could be supported further by developing tailored tools for rapid system development.
A generic structure for the integration of customized industrial gantry robots into agents of Plug & Produce automated manufacturing system
Anders Nilsson and Fredrik Danielsson
Abstract
The demand for customized products in a saturated market of trendy customers forces the manufacturing industries to transform their manufacturing from a high volume of uniformed products to low volumes and a high mix of products. High mix and low volume manufacturing is most often manually performed since existing automation solutions are only profitable for mass manufacturing, due to explicitly designed control software where the product data is implemented as low-level control code. Highly flexible automated manufacturing systems such as Plug & Produce are requested, but challenges still exist before industrial implementation. This article proposes a digitally configurable system where data for new or modified products data is configured from the perspective of the product and its manufacturing processes instead of the manufacturing resources. In a Plug & Produce system, process modules with manufacturing resources are easy to replace for new or modified products and possibly to duplicate if higher capacity is needed. Configurable multi-agent systems are proposed by several researchers as a control system for Plug & Produce. An agent is a piece of autonomous computer code that negotiates with other agents and concurrently solves tasks, distributed on parts and resources. A part is a part of a product and part agents handle manufacturing goals for the parts. Resource agents know their capability and start operating as soon as they are plugged in. Resource agents follow pluggable process modules containing manufacturing resources and act as drivers for the modules. Gantry robots have by design a naturally orthogonal coordinate system and most often lack the functionality to handle work and tool coordinate objects as standard industrial robots do. Work objects refer to a base coordinate system and tool objects contain a reference to the tool center point. These references are in this article integrated into resource agents together. A place coordinate agent has the global perspective of the Plug & Produce cell and provides the process modules with reference coordinates of the place they are plugged into. Coordinates are recalculated from a product perspective into a resource perspective by coordinate transformations built into the skills of resource agents. This structure enables the possibility for process planners in the manufacturing company to make changes on a daily basis. A test with a gantry robot Plug & Produce demonstrator was performed and presented in this article to verify the generic structure of the gantry robot control system into agents.
Navigating production automation as a service: Unveiling drivers, benefits, and challenges in manufacturing companies
Koteshwar Chirumalla, Hassanin Ali Jalil and Moris Behnam
Abstract
The integration of production automation drives innovation in manufacturing by enhancing efficiency, quality, and cost reduction. However, the capital requirements of conventional automation solutions hinder many manufacturing companies. Production Automation as a Service (PAaaS) emerges as a cost-effective alternative, offering improved flexibility and efficiency. Yet, adopting PAaaS faces challenges: a lack of expertise, awareness, and cultural resistance. This study explores PAaaS implementation in manufacturing, identifying its specific needs and challenges. Qualitative research across ten diverse manufacturing companies reveals two key drivers: technological advancement and evolving business models. It highlights four primary benefits—cost-effectiveness, flexibility, efficiency, and product quality. Simultaneously, it addresses five significant challenges—legacy system integration, cybersecurity, internet dependency, expertise gaps, and downtime risks. To aid early decision-making, the study proposes a framework covering drivers, benefits, challenges, and suitable strategies. This study contributes to the ongoing discussion on smart production and automation development by focusing on business model innovation and the pay-as-a-service approach.
A Systematic Literature Review: Key Performance Indicators on Feeding-as-a-Service
Fabio Marco Monetti, Marco Bertoni and Antonio Maffei
Abstract
In the evolving landscape of modern manufacturing, a novel concept known as Feeding-as-a-Service (FaaS) is emerging, part of the larger Automationas-a-Service (AaaS) framework. FaaS aims to optimize feeding systems in cloud manufacturing environments to meet the demands of mass customization and allow for quick responses to production changes. Therefore, it fits into the Manufacturingas-a-Service (MaaS) system as well. As the manufacturing industry undergoes significant transformations through automation and service-oriented models, understanding how FaaS fits into the other frameworks is essential. This study presents a systematic literature review with two primary objectives: first, to contextualize FaaS within AaaS and MaaS, highlighting similarities, differences, and distinctive characteristics; second, to identify and clarify the essential Key Performance Indicators (KPIs) crucial for its strategic implementation. KPIs are pivotal metrics guiding organizations toward manufacturing excellence. In this context, common KPIs focus on efficiency and quality, such as resource utilization, and error rates. Other KPIs are also crucial, such as the ones related to cost reduction and customer satisfaction. For FaaS, the most relevant include also data security, data management, and network speed. This research provides a valuable KPI framework for FaaS developers, aiding in strategic decision-making and deployment in industrial settings. It also contributes to a broader understanding of KPIs in manufacturing, which benefits both researchers and industrial practitioners. The results of the review, though, fail to address other crucial indicators for ‘asa-Service’ business, such as Churn Rate and Total Contract Value. Future research will address these limitations through methods ranging from questionnaires to practitioner interviews, with the aim of gathering the knowledge needed for real-world implementations.
A system architecture for continuous manufacturing decision support using knowledge generated from multi-level simulation-based optimization
Simon Lidberg and Amos H.C. NG
Abstract
Manufacturing is becoming increasingly complex as product life cycles shorten, and new disruptive technologies are introduced. The increased complexity in the manufacturing footprint also complicates industrial decision-making. Proposed improvements to alleviate bottlenecks do not guarantee effective problem resolution. Instead, improvement efforts can become misguided, targeting a bottleneck that affects a single production line rather than the entire site. An effective method for identifying production issues and predicting system performance is discrete-event simulation. When coupled with multi-objective optimization and multi-level modeling, production performance issues can be identified at both the site and workstation levels. However, optimization studies yield vast amounts of data, which can be challenging to extract useful knowledge from. To address this, we employ data-mining methods to assist decision-makers in extracting valuable insights from optimization data. This study presents an architecture for a decision support system that utilizes simulation-based optimization to continuously aid in industrial decision-making. Through a novel model generation method, simulation models are automatically generated and updated using logged data from the manufacturing shop floor and product lifecycle management systems. To reduce the computational complexity of the optimization, model simplification, varying replication numbers, surrogate modeling, and parallel computing in the cloud are also employed within this architecture. The results are presented to a decision-maker in an intelligent decision-support system, allowing for timely and relevant industrial decisions.
A:III Digitalization for efficient product realization
Room: C207. Session Chair: Peter Almström. Room Host: Ksenija Peggar
A Review of Modelling Methods for Manufacturing as a Service –Case Additive Manufacturing
Antti Pulkkinen, Hari P.N. Nagarajan and Juhani Heilala
Abstract
Manufacturing as a Service (MAAS) is a promising business model, especially with relatively new technologies such as cloud computing, data integration and digital twins. The article presents the characteristics of MAAS by comparing it to the characteristics of successful Software as a Service (SAAS) solution, which is open, modular, and standardized. It also describes the product, production and network data that MAAS requires to be modelled, managed and shared as a requirement for data modelling. In particular, it focuses on the modelling of product, processes and resources. Among the modelling methods, visual product-process models, matrix methods used to describe system structures, general graphical methods and methods used in system dynamics are briefly discussed. The expressive power of the methods is taken into account, and they are grouped into qualitative and quantitative modelling methods. A case study on metal additive manufacturing is presented, resulting in a generalized model of a key part of the process. The case study results with a model on how the external and internal and output parameters of melt pool influence on the output economic, quality and environmental impact characteristics. Finally, the ability of the modelling methods, the case and the MAAS features are compared. As the model is a tool for interaction between different actors and it needs to be maintained, it is concluded that qualitative and quantitative methods need to be integrated in the case of MAAS.
The Interplay Between BIM Implementation Level and Perceived Benefits: Insights from Industry Practitioners
Lina Gharaibeh, Björn Lantz, Mais Jaradat and Kristina Eriksson
Abstract
This research delves into the tangible economic impact of Building Information Modelling within the Swedish construction industry, with a particular focus on exploring the relationships among the level of BIM implementation, company size, and the perceived benefits derived from BIM. The study’s methodology involved conducting a questionnaire survey, from which a dataset of 128 responses was collected for comprehensive analysis. The study’s findings challenge prevailing assumptions by suggesting that the size of a company does not necessarily dictate its likelihood of implementing BIM. This contradicts earlier notions that larger companies have a more significant propensity for BIM adoption. Additionally, the research uncovers a positive correlation between higher levels of BIM implementation and the realization of greater benefits. This correlation underscores the potential of BIM in significantly enhancing construction project outcomes. By bridging empirical insights from industry professionals and a robust questionnaire survey, this study provides valuable contributions to the understanding of how BIM can improve performance in the construction sector. These results emphasize the importance of considering BIM’s potential benefits beyond the scope of company size and offer fresh perspectives on the dynamics between BIM implementation and perceived advantages in the construction project context.
Smart Coordination Requires Operators in the Loop
Ksenija Peggar and Monika Hattinger
Abstract
As industrial digitalization progresses and the use and application of digital technology in industrial production increases, it is tempting to view technology as the answer and solution to all the challenges that arise in production. However, does relying solely on the power of digital technological systems do justice to the complexity of today’s shop floor? We argue that despite the fact that digital technologies have the capacity to process a considerable amount of data which outperforms human computing abilities, it is crucial to apply a more holistic view and widen the scope of analysis above and beyond the immediate application of digital technologies. Thus, this study aims to explore industrial shop floor practices to increase understanding of the planning and coordination patterns. To get a thorough understanding of how planning and coordination work today and to find new opportunities, a case study approach was adopted. Data was collected in one small and medium-sized manufacturing enterprise through shop floor observations and interviews with six employees during 2022-2023. Further, we applied a coordination framework, including coordination mechanisms, for data analysis. The results show that the three coordination mechanisms Objects and Representations, Roles, and Routines are abundantly present in the case study. Moreover, two additional coordinating mechanisms were identified, Digital Technology and Context, which include a contribution to the earlier coordination framework. We argue to put the challenges that operators face into the limelight, by involving them in the planning and coordination loop.
Towards Sustainable and Technology-Enabled Engineering Psychology in Production
Lawrence Jongi, Varvara Vasdeki and Jannicke Baalsrud Hauge
Abstract
This paper explores the development of digital systems to identify and reduce cognitive stresses in contemporary manufacturing environments with increasing numbers of robots and smart machines. To achieve this, the study attempts to answer the following research question: How can technology-driven advancements in engineering psychology be leveraged to foster more productive, ethical, and psychologically supportive collaboration between humans and robots in the context of modern manufacturing environments? The study explores relevant literature to gain deeper insights into the subject succeeded by the development of a prototype composed of two digital solutions. By improving cognitive ergonomics through the detection and recognition of non-verbal cues, as well as reducing cognitive stress by providing real-time information on the positions of mobile robots, this study offers potential solutions to the social and psychological challenges of human-robot collaboration. The paper concludes with an analysis of the final prototype, a discussion on sustainability implications, and recommendations for future research. Overall, this research aims to bridge the gap between human workers and technology in the manufacturing sector, facilitating a harmonious and productive collaboration that aligns with the goals of Industry 5.0.
Evaluating an Augmented Reality Prototype for Enhanced User Guidance in an Industrial Production Context
Nicole Tobiskova, Monika Hattinger and Erik Sanderson Gull
Abstract
This study evaluates an augmented reality (AR) prototype aimed at enhancing user guidance in industrial procedures, focusing on tool change tasks. The variability in experience and skills among operators and maintenance technicians in handling machine-related requirements poses challenges to smooth operations. To address this, an AR guidance system was developed for a head-mounted display device, utilizing image, object, and gesture recognition to minimize user interaction and enhance system adaptiveness, ultimately reducing cognitive load. A user study employing video observations and questionnaires was conducted to evaluate the AR system’s impact on usability and cognitive load. Results indicate that the prototype effectively facilitated tool change tasks, providing a user-friendly experience with reduced cognitive load. The integration of image, object, and gesture recognition contributed to streamlined user guidance, minimizing the need for constant user interventions. Notably, participants experienced a fluid user experience with high usability and a moderate cognitive load, emphasizing the system’s potential in managing complex tasks. The study also highlighted the applicability of AR technology in fields beyond tool changes, such as troubleshooting, and identified a preference for an apprenticeship-style training approach among participants.
A:IV Circular Production
Room C208. Session Chair: Sabina Rebeggiani. Room Host: Atieh Sahraeidolatkhaneh
Supporting the transformation to access based business models in a circular economy with a practical model for calculating the costs of the provider
Johan Vogt Duberg and Tomohiko Sakao
Abstract
In a transformation to becoming more circular, many original equipment manufacturers (OEMs) are investigating the potential of transferring product ownership from the user to the provider, thus enabling access-based business models. Such a new model also makes the product life cycle cost borne by the provider, meaning that the OEM gains an interest in reducing the life cycle cost and prolonging the life cycle for its own benefit. In this study, a case OEM is in such a transformation and postpones the end-of-life through refurbishment and remanufacturing. However, to launch the access-based business model, the OEM needs to understand its new cash flows. Therefore, the objective of this paper is to show how an OEM has been supported by a model for calculating the product life cycle costs when transforming to an access-based business model. Through applying transdisciplinary research, a calculation model was developed in close collaboration with an OEM to calculate and visualise the product life cycle costs. The study also shows how the remanufacturing cost can be estimated based on existing repair and maintenance data. Furthermore, the importance of developing decision-making insights to persuade upper management that the new circular practices can provide boosted profitability is highlighted.
Enabling factors for circularity in the metal cutting industry-with focus on high-value Circular tools
Mohamed Elnourania, Kerstin Johansen and Anna Öhrwall Rönnbäck
Abstract
Metal cutting industry, a key sector in manufacturing, is grappling with the transition to a “net-zero industry” to mitigate climate change and reach sustainable practices. Rare and exclusive materials make recycling and reusing cutting tools more pressing and necessitate efficient circular material flows. The purpose of this research is to explore how collaboration can facilitate circularity in the cutting tool industry. It examines the involvement of stakeholders and their roles in achieving a circular lifecycle for cutting tools. To investigate the interaction between metal cutting tools suppliers and Small and Medium-sized Enterprises (SMEs), this study used a mixed-methods approach that includes data from literature, interviews, and document study. Empirical data is gathered to investigate the factors driving circularity and to identify important participants in the lifecycle of cutting tools. The study revealed challenges to the current situation including underutilization of tools due to the absence of a standardization process and subjective operator judgment, as well as lack of traceability of the tools both internally at SMEs and between the stakeholders. Moreover, by mapping the current actors, the study found cutting tool traceability, undirected decision-making throughout tool lifecycles, and limited awareness of circularity dimensions are key challenges. To handle these challenges. 9Rs circular economy framework used to investigate the possible role of collaboration emerges as a vital enabler for circularity, with SMEs playing a significant role. Moreover, the involvement of machine operators, often overlooked actors, is found to be crucial in influencing circular outcomes. Digital solutions and collaborative strategies that involve CNC machine suppliers and intermittent refurbishing business are pivotal in overcoming the challenges identified, namely, traceability and human subjectivity in tool condition assessment. The study demonstrates that technology providers, intermediary refurbishing businesses, SMEs and other stakeholders operating in the metal cutting tools sector must be involved throughout their lifetime to avoid suboptimal results, exchange information, and inspire industrial actors to support the circular economy.
Enabling circular and reconfigurable machining system within the automotive industry– a multiple case study
Carin Rösiö, Filip Skärin, Patrik Gustavsson and Ann-Louise Andersen
Abstract
To shift the focus from a reactive development approach to a purely proactive approach is a comprehensive and decisive challenge. Reconfigurable manufacturing principles offer a new perspective that emphasizes adaptability over obsolescence. This paper aims to explore how automotive industries include reconfigurability and circularity in production system design to prolong the production system lifetime. In a multiple case study within automotive industry the long-term view in machining system development has been investigated. The results show that the companies try to leave the linear approach behind to look beyond the specific project boundaries and enable a system to be reused over time. There is an awareness of the importance to adopt long-term approaches to achieve a circular mindset and the study reveals that machining systems are characterized by a higher flexibility and higher degree of standardization to enable turbulence in requirements. Still, there are methods required to consider future needs, strategies, and technologies to enable reconfigurable and circular systems.
Circular strategies in the Swedish furniture industry – a business modelling approach
Mirka Kans, Chamirangika Madushani Hetti Arachchige and Dan Paulin
Abstract
The interest in circularity and circular strategies is increasing in the furniture industry. Wood is a climate-smart and sustainable material, partly because it has many environmental advantages compared to other materials such as plastic or metal, partly because it is a highly renewable material. Today, the technical lifespan of wood products such as furniture is not fully utilized. Today, the technical lifespan of wood products such as furniture is not fully utilized, which could be explored through circular strategies. By extending the life of products, components, and materials, the environmental impact could be significantly reduced. However, several challenges have been identified that hinder the establishment of circular strategies. Inconsistent policies and obstructive legislation, high initial costs and long payback periods, low consumer awareness, and lack of collaboration in the value chain are examples of main challenges. The research question addressed in this paper is How to facilitate the circular development of the Swedish furniture industry by promoting circular business models? This paper discusses the barriers and drivers of circularity with specific focus on the characteristics of the furniture industry in the Swedish context. A conceptual approach for establishing circular strategies in the furniture industry based on the 10R model, the business model canvas, and the product-service system approach is proposed. The approach facilitates the identification of relevant circular strategies that can be developed into circular business models. The paper concludes that circular strategies and business models entail positive economic, environmental, and social sustainability impacts for customers, companies, as well as on the society, but to achieve the benefits, organizational and technical solutions addressing the barriers on organizational, industry, and societal level must be developed. Circular business models are a way to overcome several of the barriers while promoting industrial and value chain collaboration.
Integration of Circular Value Chains and Digitalization: A Focus on Lithium-ion Battery Material Value Chain
Hossein Rahnama,AMA, Kerstin Johansen and Anna Öhrwall Rönnbäck
Abstract
Circular value chains, driven by sustainability goals and resource efficiency, are now central in industrial strategies. Simultaneously, digital technologies transform business models and accelerate the shift towards circular economies. This paper explores circular material flow for the electrification of the vehicle fleet, focusing on the Lithium-ion battery value chain. In the paper, a conceptual model integrating digitalization is developed and evaluated to enhance efficiency and product innovation. The paper reviews the lithium-ion battery value chain literature and investigates digitalization potentials for circular business models. A conceptual model is presented in this study to represent the intricate relationship between each stage of the value chain and the concept of circularity while considering the carbon footprint and complexities associated with the implementation of digitalization.
A:V Industrial transformation for sustainability E
Room: C123. Session Chair: Anna Granlund. Room Host: Yongcui Mi
An introductory study of the sustainability transition for the aerospace manufacturing industry
Pauline L. Y. Léonard, Sophie I. Hallstedt, Johanna W. Nylander and Ola Isaksson
Abstract
This paper explores the needs and clarify the sustainability challenges in relation to complex lifecycles within the aerospace field. It is an introductory study to understand how to improve the sustainability performance of aerospace solutions and aim to propose a comprehensive sustainability transition roadmap for the Aerospace industry in further research work.
Society is increasingly demanding that the aviation industry adopt more sustainable practices, resulting in the formulation of new regulations and policies to limit the sustainability risks of this strategic industry. Existing regulations, such as the EU’s Green Deal and the EU’s critical raw materials act, are already impacting the Swedish aerospace manufacturing industry. Furthermore, circular economy is gaining significant attention in the manufacturing industry in general and is increasingly considered in aerospace.
This exploratory and descriptive research is conducted with support of Swedish Aerospace manufacturers and aim to cover real industrial projects with products at different stages of development. The interviewed companies operate within both civil and governmental aerospace sectors, encompassing the entire spectrum of product development, from radically innovative technology introductions to enhancements made to existing systems and components.
This paper highlights current challenges and several focus areas on which the aerospace manufacturers have started to work on and will have in focus for the next 5-10 years ahead. Differences in approach have been identified between early product development phases with radical innovations and more advanced and mature product development. The stakes and priorities are different and it is reflected on how the companies are working with sustainability today. There is a need to balance efforts between developing the right future products, and also improving current ones, to lead the sustainability transformation in the aerospace industry.
Availability and need for climate footprint and resilience data from suppliers in automotive supply chains
Martin Kurdve, Kristin Fransson and Patrik Jonsson
Abstract
This paper explores the challenges and opportunities of managing supply chain data for environmental sustainability and resilience in the automotive and vehicle manufacturing industry. It presents empirics from measuring and improving the climate footprint, based on data from interviews and workshops with original equipment manufacturers (OEMs) and suppliers, and compares concepts of resilience of supply chains. The paper focuses on the early phases of supply chain interaction, such as supplier selection and request for quota, when specific product data is often unavailable or estimated. It discusses the trade-offs and conflicts between the needs and availability of climate footprint and related supplier data, such as localization, energy supply, material supply and transportation. It also highlights the importance of data regarding recycled contents, materials, and energy in the supply chain. The paper is connected to projects funded by the EU and Vinnova that aim to enhance the competitive sustainability and resilience of the industry.
Integrating Smart Production Logistics with Network Diagrams: A Framework for Data Visualization
Yongkuk Jeong, Erik Flores-Garcìa, Juhee Bae and Magnus Wiktorsson
Abstract
This paper introduces a framework that integrates smart production logistics (SPL) with network diagrams. This integration enhances visibility in the material and information flow within the manufacturing sector, thereby adding value through data visualization. Drawing from a detailed case study in the automotive industry, we outline the essential components of network diagrams that are tailored to depict spatial-temporal data linked with material handling processes in an SPL context. This integrated approach presents managers with a new tool for optimizing planning and executing tasks related to the transport of materials and information. Furthermore, while the framework brings about significant technological progress, it also emphasizes the managerial implications of SPL data visualization. In particular, it highlights its potential to foster informed decision-making, resource optimization, and strategic forecasting. The paper also discusses prospective research avenues, stressing the importance of dynamic diagrams that decode complex patterns from digital data and the incorporation of sustainability metrics in SPL assessments.
Making the Digital Strategy a Bridge between Industry 4.0 Initiatives and the Business Plan – Reports from two Case Studies towards Manufacturing SMEs
Mattias Strand and Magnus Holm
Abstract
In this paper we discuss the results of two extensive case studies targeted towards Swedish SMMEs, partly aimed at investigating the current state of practice regarding the strategic work in the companies and its alignment to digitalization initiatives. The case studies were conducted during 2022 and 2023 and includes a vast empirical material, including several site visits, more than 30 interviews, several meetings with the managerial boards of the two companies and workshops, as well as studies of strategic document, product portfolios and Gemba walks. The paper presents a suggestion for how to formulate a one-page digital strategy, which aligns the digitalization initiative with the overall strategy of the company, as well as a vision for the digital transformation initiative. In addition, the one-pager also includes prioritized stakeholder groups, expected effects and prioritized activities. Moreover, we also motivate the reasons behind a one-pager, as well as the topics included therein. Finally, we give some ideas for future work, including the importance of implementing the one-pager in more companies, as a way to further validate its applicability and long-term influence on and relevance for the strategic work in SMMEs.
A Methodology Using Monte-Carlo Simulation on Nanoindentation Deconvolution for Metal Classification
Juan Manuel Bello Bermejo, Christina Windmark, Oleksandr Gutnichenko and and Jan-Eric Ståhl
Abstract
This paper investigates a methodology for the precise statistical deconvolution of hardness properties within various metallic matrix multiphase materials. The central focus is on accurately characterizing mechanical behaviour in the context of complex materials. To meet these objectives, we implemented an approach involving nanoindentation analyses of the selected materials. This technique allowed for the creation of material profiles based on micromechanical properties. Statistical cumulative density function (CDF) deconvolution was employed to disentangle the complex distributions of multiphase material hardness using crossvalidation. Throughout the course of this study, several multicomponent CDF combinations were tested, including Weibull, Exponential, and Gaussian distributions. This approach challenges the conventional practice of assuming multiple Gaussian distributions of hardness, revealing the limitations of this approach. In addition, Monte-Carlo simulations were harnessed to generate probability density functions (PDFs) that capture the intricate footprint variations in hardness profiles. By implementing our methodology, we strive to offer a comprehensive and refined approach to materials analysis. This potential for differentiation has the significant implication of investigating the impact of impurities and trace elements on the mechanical properties and thus, machinability of metal materials. The ultimate aim is to enhance their recyclability, thereby advancing the principles of the circular economy and contributing to the sustainable development goals. Our study thus underscores the profound impact of material analysis on environmental sustainability and the efficient use of resources, while offering a fresh perspective on the role of statistics in materials science.
Workshop A, April 24th 11:00–12:00
Room: Entré AIL
Digitalization for Sustainable Manufacturing
Remanufacturing plays a crucial role in today’s pursuit of a Circular Economy. However, implementing successful remanufacturing within an industrial value chain is very challenging due to the process optimization, design considerations, and business model adaptation involved.
The RESTORE project addresses those challenges and will be a central topic of this workshop. The workshop includes a short presentation of the project, group work, as well as the presentations of group discussions.
Workshop Leader: Jule Wegen, EIT Manufacturing