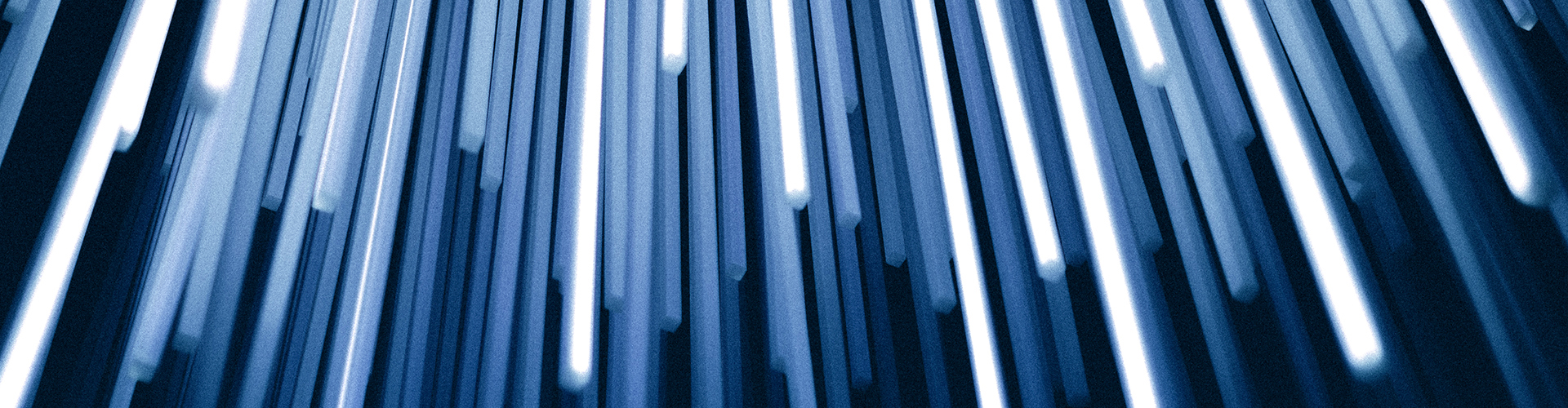
Paper sessions & workshop C
Paper sessions C:I-C:IV April 25th, 09:45-10:45
C:I Sustainable Manufacturing
Room: C118. Session Chair: Tomohiko Sakao. Room Host: Kameswaran Swaminathan
Sensitivity analysis of Colding’s Equation in side milling of medium carbon steel C45 E
Fredrik Kantojärvi
Abstract
This work focuses on reducing the experimental need for creating a reliable tool life model for a data set of 46 tool data points with its resulting tool life for a single-tooth side milling application in medium carbon steel, C45 E. Based on the data set, 615 180 unique tool life models are created using Colding’s equation. This is achieved by creating models using different unique subsets of the complete data set where the cardinality is varied from 7 to 43. The paper shows that the improvement from adding more data points to the modelling are neglectable after 34 data points are included in the modelling if a maximum absolute model error ≤ 9% is sought. Furthermore, it is shown that the prediction error increases when extrapolating outside the range of equivalent chip thickness and cutting speed used for the modelling work compared to an interpolative error within the range. By carefully planning the experimental set-up by maximising the cutting speed and feed range decreases the risk of creating a non-relevant model where the prediction error increases when located outside the modelling range.
Towards in-line measurements of sawn wood surfaces
Sabina Rebeggiani, Vijeth Reddy, Linus Olofsson and Magnus Fredriksson
Abstract
Metrology and characterisation of products' functional surfaces are of key importance in smart and sustainable manufacturing. By proper measures of resulting topography and dimension at the micro-cm level, higher process control can be achieved, leading to more efficient production with products closer to defined targets. Commercial surface metrology systems for lab- and in/on-line applications have increased in the last decades, but the wood sector has not yet benefited from this development. A better understanding of sawn wood topography combined with smart online metrology systems is expected to lead to a substantial reduction of waste in sawmill production, both by transforming waste pieces and sideboards into engineered wood products and by optimising the sawing process (e.g. by using thinner saw blades and reduced tolerances). It would also open new design possibilities and challenge the construction sector to replace today’s materials with renewable raw materials. Additionally, sawmills will be less dependent on incoming timber dimensions. This study is the first step towards a better understanding of sawn wood topography and how relevant surface features can be detected and analysed to enable the next generation of functional wood surfaces for various applications. By identifying the measuring instrument’s capability to capture surface topographical features of sawn wood, this paper discusses the requirements for efficient measurement techniques. It opens for future implementation of machine learning algorithms to in-line monitor and control the machining process. All tested metrology techniques showed promising results. To capture machining marks, the instrumentation needs to have lateral resolutions on the um level and a measurement area covering some cm; thus, the laser scanning system seemed to be a good compromise.
Strategies for Effective Chip Management in Machining of Ductile Cast Iron
Alexander Jönsson, Giacomo Carlo Ferdinando Aliboni, Christina Windmark and Jan-Eric Ståhl
Abstract
A continuously growing and mutating market with increasing demands on environmental sustainability, illuminated by unraveling environmental threats, highlights the need for greater resource efficiency in modern manufacturing industries. Machining has become pivotal in the pursuit of sustainability given its superior efficiency in manufacturing of metallic products.
In theory, the efficiency of a machining operation is dictated by the material removal rate and chip formation behavior. However, this may also present additional challenges as chips can be difficult to evacuate from the workpiece, and cause chip carryover. Chip management aims to contain manufacturing costs by addressing this issue and simultaneously pursuing higher machining efficiency. Persistent chips trapped in internal cavities is particularly challenging and can affect quality, and result in costly re-manufacturing, scrapping of portions of produced volume. Effective chip management strategies is therefore crucial to avoid these problems. While there is established research on machining theory and chip removal, proposed solutions are often focused on a specific implementation and lack a holistic perspective on the phenomenon. This study aims to fill this gap in the knowledge by providing a strategic and practical application to tie together information that would otherwise be disaggregated. A case study was conducted to investigate the role of machining, and identify the source of chip carryover and its effect on subsequent production stages. Practical verification demonstrated the effectiveness of the proposed interventions in reducing production costs by decreasing the cycle time and reducing waste, and improving product quality. The future of sustainable manufacturing processes relies on the adoption of strategies and interventions that contribute to the efficiency and sustainability of the manufacturing industry. This study provides a valuable contribution to this effort.
C:II Smart Production and Automation
Room C120. Session Chair: Andreas Archenti. Room Host: Karhik Vaidyalingam Arumugam
Exploring Production System Knowledge Graph Applications Using a Simulation Framework
Martin Birtic, Richard Senington and Anna Syberfeldt
Abstract
Knowledge graphs are generating significant interest in industry and research. These graphs can be enriched with data to represent aspects of production systems such as their structure, component interrelationships, and conditions. This provides opportunities to gain insights into system behavior, performance, and states. Such insights could potentially be leveraged by a wide range of technologies for a multitude of purposes and applications such as system control, process optimization, and informed decision making. However, the existing literature addressing industrial applications of knowledge graphs related to production systems remains limited in scope and depth. This underscores the importance of developing methods for exploring the potential use and implementation of knowledge graphs in such systems. The primary focus of this study centers on facilitating such exploration by developing a virtual commissioning simulation framework. A modular production system is modelled that leverages physics, moving product dynamics, and incorporates authentic PLC and robot programs. A knowledge graph is integrated and enriched with data representing various aspects of the system. An application is developed to facilitate product routing and prioritization. A serviceoriented approach is used that leverages graph data processing and exchange for service registration and matching. System simulations are conducted and subsequently the framework is evaluated for outcomes and findings. This study demonstrates the successful design and implementation of a production system simulation framework that uses knowledge graphs for system functionality. It demonstrates the exploration of knowledge graph applications through the development of a modular and service-oriented system that includes system functionality supported by the graph. The results highlight the potential of simulation suggesting its capacity for valuable exploration regarding potential applications of knowledge graphs within production systems.
Sources of Complexity in the Development of Digital Twins in Manufacturing
Adrian Sanchez de Ocanã, Jessica Bruch and Ioanna Aslanidou
Abstract
Digital twins have emerged as a critical technology to enable smart production. Digital twins can enhance the current production system by optimizing the current setup and facilitating decision-making based on facts rather than gut feeling. Despite the numerous benefits explored, digital twins have faced many challenges in developing and implementing production systems. Their complexity is causing a lack of digital twin implementations in the production system. This complexity can be traced back to physical and virtual entities and the digital twin development process. By conducting a case study in a global manufacturing company, this publication explores the sources of complexity when developing digital twins. The findings are organized around the digital twin development steps and their corresponding complexity. The number of different types of entities being modeled, the choice of the modeling approach, modeling low-frequency events, emergent phenomena, and the unpredictability and variability of the manufacturing process are all examples of structural and dynamic complexity that have been found to impede success in digital twin applications. This research has implications for managers who are involved in the development of digital twins in their organizations. It can help with methodological guidance when dealing with an undefined and complicated process of digital twin development.
Enhancing Manufacturing Flexibility through Automation Packaged Solution (APS): A Case Study Approach
Ghazaleh Azizpour, Milad Ashourpour and Kerstin Johansen
Abstract
The use of automation is reshaping tasks in diverse industries, leading to increased productivity and efficiency. The manufacturing sector, in particular, has enjoyed significant advantages from automation, including enhanced quality control, waste reduction, and improved worker safety. However, while the advantages of automation in manufacturing are clear, the implementation of automation in complex manufacturing processes is not without its challenges. One such challenge is ensuring adaptability to new products. In addition, the initial investment for automation in manufacturing processes often presents a significant financial difficulty, particularly in the areas of engineering, design, and programming. The aim of this paper is to provide flexible solutions that can be adopted on any manufacturing line within a short timeframe. This type of flexible solution is referred to as Automation Packaged Solution (APS). APSs involve the deployment of robotic systems and vision technologies to automate specific tasks. The key advantage of these flexible solutions is their ability to adapt to the introduction of new products into the production line without the need for extensive reengineering and reprogramming. The approach involves designing detailed computer simulations based on the initial solutions and bringing the solution to life through an offline commissioning method. In this research, a case study was conducted at a manufacturing plant in Sweden, where two APSs were introduced to their assembly line: Precise screwing and accurate application of product labeling. These APSs play a crucial role in facilitating rapid upgrades and adjustments to automation systems, especially considering the diverse range of product models. This adaptability reduces the time and resources required for reconfiguration and contributes to enhanced operational efficiency, cost-effectiveness, and more sustainable manufacturing solutions. Moreover, it opens up the possibility of transferring these APSs to another production line if the need arises.
C:III Digitalization for efficient product realization
Room: C207. Session Chair: Ola Isaksson. Room Host: Lina Gharaibeh
Knowledge Graphs for Supporting Group Decision Making in Manufacturing Industries
Ludwig Mittermeier, Richard Senington, Sunith Bandaru and Amos Ng
Abstract
Group decision making is traditionally a human-centered process, where communication, synchronization and agreement are driven by the stakeholders involved. In the area of multi-objective optimization (MOO), this becomes a challenge, because MOO usually produces a large amount of trade-off solutions that need to be analyzed and discussed by the stakeholders. Moreover, for transparent group decision making, it is important that each decision maker is able to trace the entire decision process – from associated data and models to problem formulation and solution generation, as well as to the preferences and analyses of other decision makers. A graph database is capable of capturing such diverse information in the form of a knowledge graph. It can be used to store and query all dependencies and hence can support complex decision-making tasks. Further advantages are the inherent suitability for visualization and the possibilities for pattern matching, graph analytics and, if semantically enriched, to infer new connections in the graph. In this paper, we show how such a knowledge graph can be used to support more transparent and traceable decision-making activities, particularly when multiple stakeholders with differing preferences or perspectives are involved.
Virtual commissioning during the manufacturing equipment procurement process: From an industrial expert point of view
Kristina M. Eriksson, Johan Vallhagen and Andreas Rudqvist
Abstract
The procurement process of investing in new manufacturing equipment can be time-consuming and complex. This is especially prevalent in manufacturing companies specializing in production of cutting-edge low volume components. The focus of increased digitalization in the era of industry 4.0 has brought to light novel technologies, such as virtual commissioning, factory scanning, digital twins, and their respective digital models. The aspects of virtual commissioning in relation to the procurement process were investigated through a case study at a manufacturing company. The data collection was explorative and qualitative, including mapping of the case company procurement process and four in-depth interviews with industry experts, performed during spring 2023. The industry experts were selected to enlighten the procurement process from different angles, i.e., project management, electrical installations, robot programming, and maintenance. The findings from the study are fourfold. First, the existing procurement process was mapped and holistically explained from the viewpoints of different work functions. Secondly, improvements to the current procurement process were identified. Thirdly, the current use of virtual commissioning in the procurement process was brought to light. Finally, challenges and possibilities for using virtual commissioning in the procurement process were brought forward. The conclusion displays possible improvements to flow and time aspects of the procurement process and thus application of virtual commissioning is worthwhile to consider. However, the industrial experts, taking part in the interviews, bring forth certain skepticism and challenges of using virtual commissioning. Thus, to move forward, it is important to proactively engage experts and other employees concerned with sought development. This emphasizes the industry 5.0 perspectives of humans’ interaction and critical thinking when facing challenges of industrial digitalization. Future research is therefore encouraged to involve joint discussions between industrial experts in focus group settings and extending the study to incorporate more functions i.e., managers and machine operators.
VR interaction for efficient virtual manufacturing: mini map for multi-user VR navigation platform
Huizhong Cao, Henrik Söderlund, Mélanie Despeisse, Francisco Garcia Rivera and Björn Johansson
Abstract
Over the past decade, the value and potential of VR applications in manufacturing have gained significant attention in accordance with the rise of Industry 4.0 and beyond. Its efficacy in layout planning, virtual design reviews, and operator training has been well-established in previous studies. However, many functional requirements and interaction parameters of VR for manufacturing remain ambiguously defined. One area awaiting exploration is spatial recognition and learning, crucial for understanding navigation within the virtual manufacturing system and processing spatial data. This is particularly vital in multi-user VR applications where participants' spatial awareness in the virtual realm significantly influences the efficiency of meetings and design reviews. This paper investigates the interaction parameters of multi-user VR, focusing on interactive positioning maps for virtual factory layout planning and exploring the user interaction design of digital maps as navigation aid. A literature study was conducted in order to establish frequently used technics and interactive maps from the VR gaming industry. Multiple demonstrators of different interactive maps provide a comprehensive A/B test which were implemented into a VR multi-user platform using the Unity game engine. Five different prototypes of interactive maps were tested, evaluated and graded by the 20 participants and 40 validated data streams collected. The most efficient interaction design of interactive maps is thus analyzed and discussed in the study.
C:IV Integration of education and research
Room C208. Session Chair: Mirka Kans. Room Host: Ali Eskandari
Does the Improvement in AI Tools Necessitate a Different Approach to Engineering Education?
Jannicke Baalsrud Hauge and Yongkuk Jeong
Abstract
The integration of artificial intelligence (AI) into the manufacturing sector introduces new challenges and demands for the engineering workforce in the evolving European economy. This paper investigates how advancements in AI tools, especially in manufacturing, necessitate a shift in engineering education to equip graduates with relevant skills and ethical understanding. While AI is not new to manufacturing, its ongoing development and increased accessibility bring forth fresh challenges related to required competencies and ethical considerations. Furthermore, this work explores the potential of incorporating recent AI tools, such as ChatGPT and other generative adversarial networks, into engineering education. This is illustrated through a case study of a master’s level digitalization course. In this course, AI tools aimed to help students bridge their programming knowledge gaps and educate them on ethical AI use, providing a model adaptable to lifelong learning courses in the field. This inquiry also addresses the broader concerns related to AI misuse in academic settings and the subsequent difficulties in plagiarism detection and accurate learning outcome assessment. The discussion does not argue against AI adoption but emphasizes managing its inadvertent impacts on the industry and society. By integrating emerging technologies and their ethical use into the curriculum, the engineering education system can better align with the shifting demands of the workforce in an increasingly digitalized manufacturing landscape.
Challenges and Enablers in Recruiting Maintenance Employees
Marcus Bengtsson and Lars Berglund
Abstract
Manufacturing maintenance has always undergone change and development. With Industry 4.0-related technological development, increasingly more complex machining equipment, and an increased focus on sustainability, maybe more so today than ever. This has led to an increased difficulty in finding competent maintenance employees to recruit. Simultaneously, it increases the need for continuous competence development to retain the existing work force up to date with the challenges of future development. The introduction of these new technologies and demands does not reduce the need of competence in basic maintenance skills though, but rather adds new areas of needed competence, making the maintenance profession increasingly more complex. This paper will, through an interview study of maintenance managers in an international manufacturing company located in nine countries, delve into the issues and present both challenges and enablers in how to work with recruitment and competence development within maintenance.
Workshop C, April 25th 09:45-10:45
Room C123
Future education and training of product development, design and innovation
The societal and industrial needs for product development, design and innovation is undergoing rapid and urgent change. In order to be pro-active and adapt to this transition, organisations and individuals need not only to learn, but to re-learn. Competence development and training, life-long learning, upskilling and general adaptation of mindset and capabilities will be important across academic, public and industrial sectors. In this workshop, we collaborate using design thinking methods to explore opportunities for this transition to happen, and identify potential pathways towards the future.
Workshop Leaders: Professors Anders Warell, Lund University and Anna Öhrwall Rönnbäck, Luleå University of Technology
Organizer: Product Development Academy (PDA)